RAW MATERIALS
Cement plants seek to improve their efficiency in the production process to reduce the consumption of natural resources
From the manufacturing process, two products are the result: clinker and cement, although this second – cement – is the result of grinding the first along with additions. The basic material to make clinker is calcium carbonate, which is mostly obtained from limestone or marl, which are a combination of limestone and clay.
Continuing with the principles of the so-called “circular economy”, this strategy consists of “doing more with less”. Catalan cement factories seek to improve their efficiency in the production process to reduce the consumption of natural resources. The ways that allow this savings are the use of by-products as raw material for clinker and through additions in the cement manufacturing.
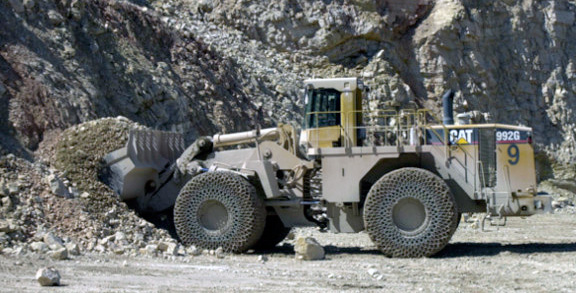
THE ENVIRONMENTAL ADVANTAGES OF MATERIAL VALORIZATION
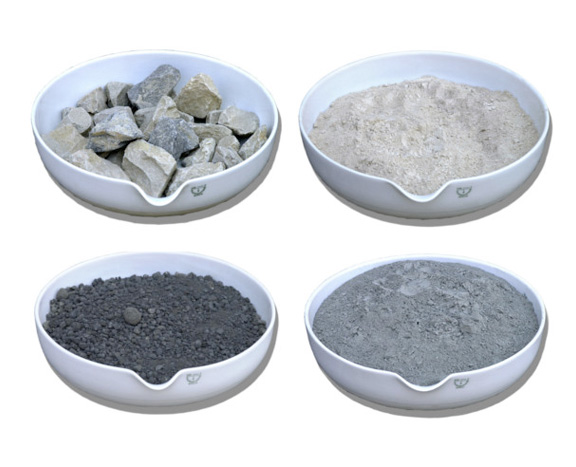
Cement plants recycle a large number of industrial by-products, either to partially replace raw materials or as cement additives, to avoid that the final destination of these wastes ends in landfill. The cement manufacturing process enables recycling waste in two ways:
- As substitutes for raw materials, when industrial by-products are mixed with natural materials (limestone and marl) before entering the kiln, which reduces the resources extracted from the quarries. The most commonly used raw materials substitute in Catalonia are pyrite ashes (which have a high content of iron), paper slurries (calcium carbonate), smelting sands (silicic oxide) or demolition waste (calcium or siliceous). Construction debris can be used as a substitute for raw materials, but requires a previous separation process.
- As additions to cement, when industrial by-products are milled or mixed in limited quantities with cement, to modify their properties, such as rate of hardening, resistance levels or durability to specific aggressive agents such as sea water or sulfates are achieved. The factories use residues with hydraulic or pozzolanic properties as additions: fly ash from coal-fired power plants, blastfurnace granulated slags, industrial pozzolans, industrial plaster…
ADDITIONS REDUCE CO2 EMISSIONS
Since the additions are not calcined in the kiln but are added to the clinker, there is a saving of fuel for each tonne of cement produced and thus a decrease in CO2. emissions. Specifically, for every tonne of clinker saved thanks to substitution by additions, the amount of CO2 emitted into the atmosphere is reduced by 0.9 tonnes.
These types of alternative materials do not imply any increase in atmospheric emissions, have no impact on workers’ health or the environment and do not affect the quality of the final product. However, the use of additions to clinker is not unlimited, since it is regulated for each type of cement by the standards of quality of the product, collected in the UNE and UNE-EN standards.
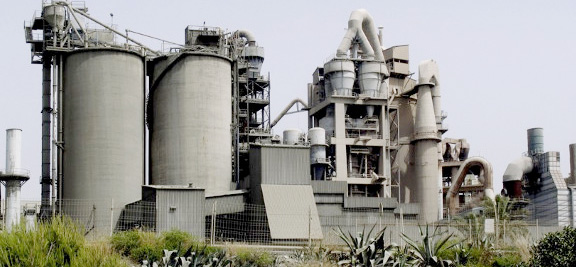
BENEFITS OF WASTE RECYCLING IN THE CEMENT MANUFACTURING PROCESS

Decreases the need to extract natural resources

Reduces exploitation of quarries

Reduces dust and noise emissions

Take advantage of the resources destined as waste without added impacts

Manages waste that requires solutions different to landfill at a competitive price

It saves energy, since it allows to manufacture less clinker to obtain the same amount of cement thanks to the additions

Reduces emissions of greenhouse gases