CIRCULAR ECONOMY
The cement sector has been a pioneer in Europe in the application of energy efficiency strategies
Essentially, circular economy is an efficiency strategy: “doing more with less.” It consists in reducing both the consumption of materials in the production phase of goods and minimizing the generation of waste. In this way, it goes from a linear flow of materials (resource-product-waste) to a circular flow (resource-product-resource recycled). And all this, coordinated with the progressive abandonment of the use of fossil fuels (that are polluting and expensive) by renewable energy. It is the combination of these two policies that arises the concept of energy utilization of the residues that neither could be avoided nor can be reused or recycled. The biosphere is the great beneficiary because, apart from reducing the consumption of fossil fuels, there is a drastic drop in landfills.
The cement sector has been a pioneer in Europe in the application of the principles of circular economy. Factories have long used, for example, building debris or metal slag as raw materials for their product. It is the so-called material valorization, and serves to integrate wastes into the productive cycle that, otherwise, would go to landfills, harming natural environments. Also in the energetic use of waste, cement companies are leaders, based on the experiences of leading countries in the environmental protection like Germany, Holland or Austria. And they have been doing it since the 1980s, obtaining heat for their kilns by burning a range of residues ranging from forest debris to plastics, to old-fashioned tires or meat-based meals.
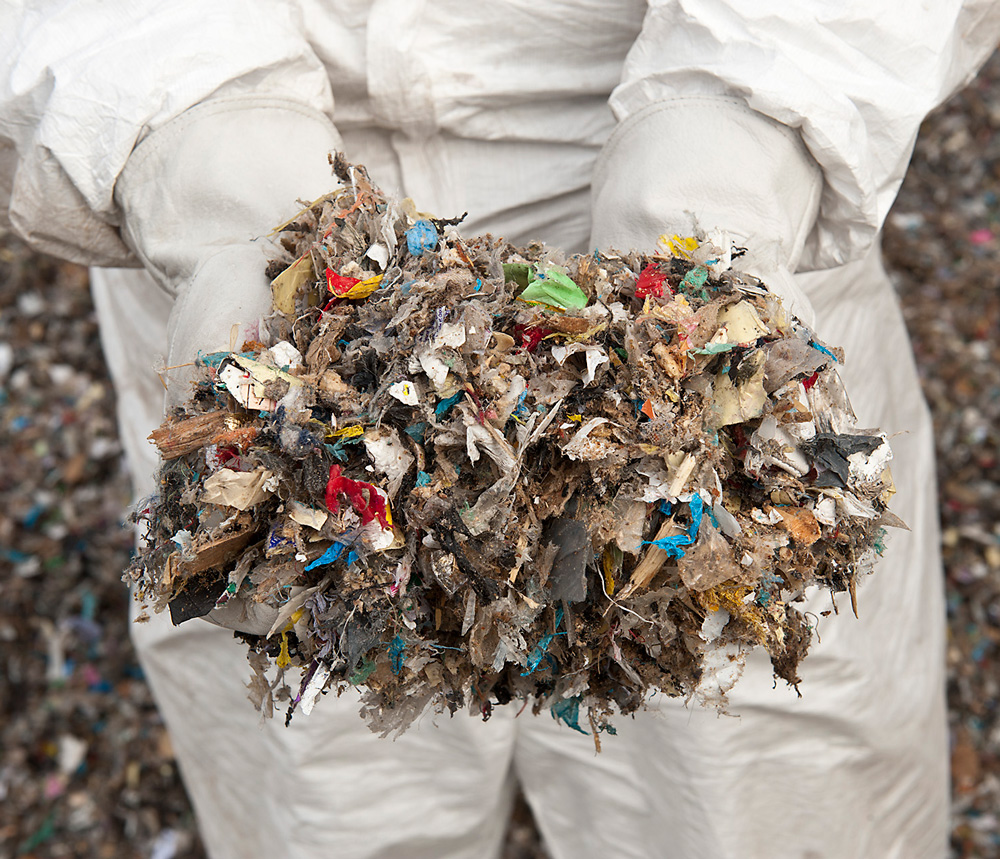
THE ENVIRONMENTAL ADVANTAGES OF THE ENERGETIC USE OF WASTE
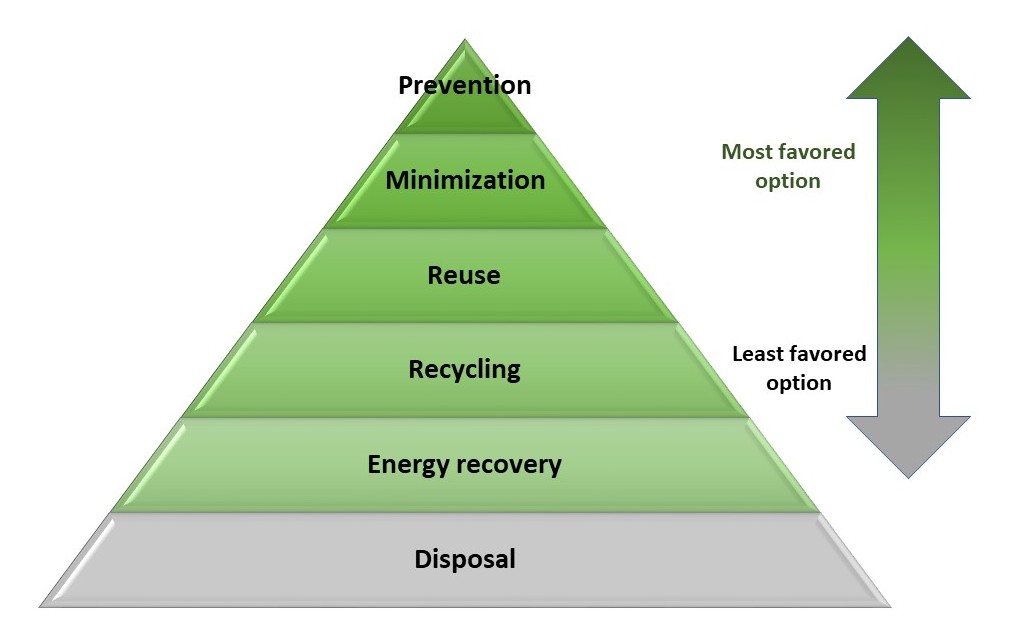
Thermal exploitation of waste is a source of competitiveness for companies, as the cost of this energy is lower than fossil fuels. But above all, it represents an environmental contribution of the first magnitude:
- Reduces CO2 emissions and allows to slows climate change
- Reduces landfills, which avoids the risk of contamination in soil and air, and of fire from the discharged wastes
- Decreases consumption of non-renewable fossil fuels
- Given that it is carried out in the area of territorial proximity, mitigates negative effects by air or nature derived from emissions from transport of fuels from other continents
The Catalan cement industry is scrupulous with energy recovery from waste, as it fully respects the hierarchy of management of these products: Energy recovery is only a policy of action to be applied when the generation of waste can not be avoided, or its reuse or recycling. This is also a firm commitment of the industry, which fits perfectly with the circular economy strategy.
A SAFE PRACTICE FOR PEOPLE AND THE NATURAL ENVIRONMENT
Human health and air quality assurance in energy recovery in clinker kilns is supported by a large and documented scientific literature, the result of research and fieldwork of universities and public and private institutions in Europe and North America. All studies conclude that there is no significant change in the parameters of emitted gases during energy recovery from residues with respect to the emissions produced using fossil fuels.
These studies include:
- Towards a better exploitation of the technical potential of waste-to-energy. JRC Science for Policy Report 2016. European Commission
- Karstensen, K.H. 2008. Formation, release and control of dioxins in cement kilns. Chemosphere, 70
- Pegg, m.j. Amyotte, P.R., Fels, M., Cumming, C.R. & Poushay, J.C. 2007. An assessment of the use of tires as an alternative fuel.
- Lavall, A., García, A., González, C., Liebert, C. & Perret, J.F. 2010. Estudio sobre las emisiones y su posible efecto sobre el medio ambiente y la salud en el entorno de plantas cementeras. Cemento Hormigón, 398
- CANTOX Environmental, Mississauga, Ontario. Literature Review & Assessment of Public Health Impacts of Alternative fuels used in the Cement Industry. Report to the Cement Association of Canada, September 2006
- Abad, E., Martínez, K., Caixach, J. & Robera, J. 2004. Polychlorinated dibenzo-p-dioxin / plychlorinated dibenzofuran releases to the atmosphere form the use of secondary fuels during clinker formation. Environmental Science & Technology, 38
- Schneider, M. 1996. PCDD / F emissions from Germany cement clinker kilns. Organohalogen Compounds, 27
- Richards, J., Goshaw, D., Speer, D., & Holder, T. 2008. Air emissions data for portland cement pyroprocesing operations firing tire-derived fuels. PCS R & D Serial, 3050
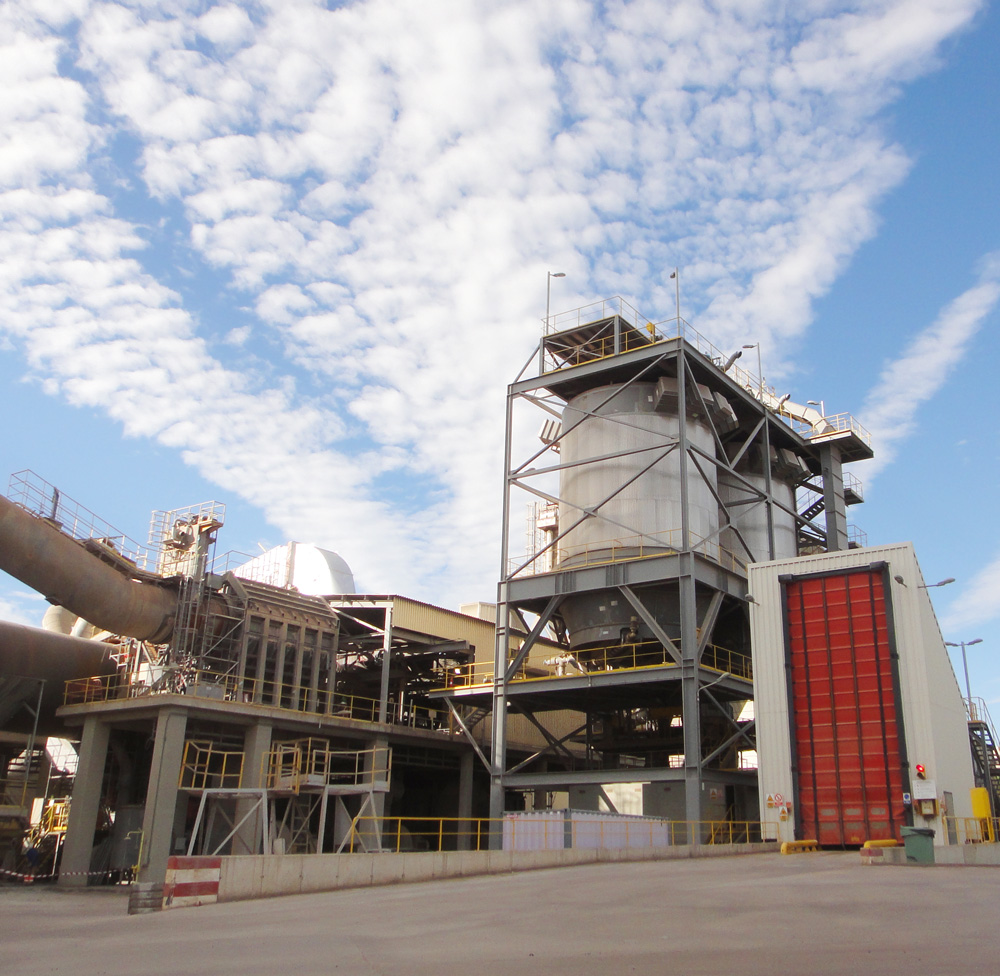
In addition, the emissions of gases from energy recovery are continuously monitored by the Administration. And all the accumulated historical series show that they are always below the limits set by European legal regulations.
AN APPROPRIATE TECHNOLOGY TO GUARANTEE SOCIAL, ENVIRONMENTAL AND BUSINESS BENEFITS
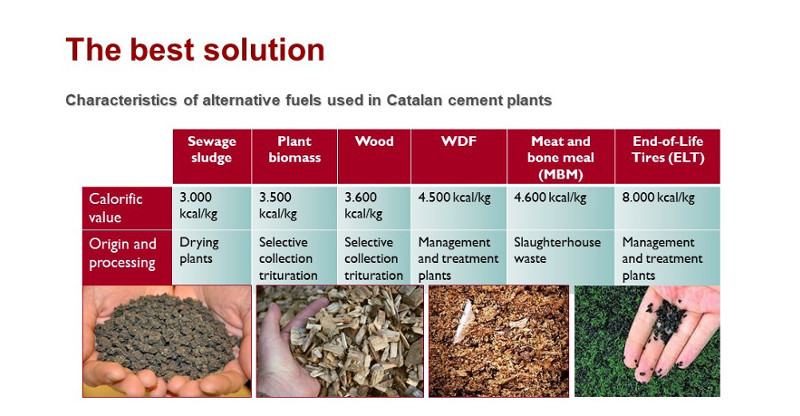
There are two major advantages of cement factories in the process of energy recovery from waste, especially when compared to conventional incineration plants that are dedicated to produce energy with them. On the one hand, because of its benefits: the materials inside a cement kiln burn more time and at a higher temperature, which facilitates the destruction of the organic compounds in the fuels. On the other hand, ashes and slag that are generated during the burning process are integrated into the manufactured product, which is not the case with the incinerators, which produce energy, but generate a new waste to be managed. In cement plants, the concept of circular economy takes its maximum flight.
In summary, the energy valuation of waste is a practice:
- Safe for health
- Beneficial for the Environment
- Compatible with waste hierarchy
- Useful for society
- Source of competitiveness for companies
- Essential in the fight against Climate Change